- Home
- Company
- Industries
- Pharmaceutical Industries
- Food and Chemical Industries
- Agro industry
- Cement Industries
- Foundry Industry
- Petrochemical Industry
- Detergent Industry Insights: Sparking Innovation
- Steel & Non-Ferrous Industries
- Distillary & Brewery Industries
- Biscuit and Confectionary
- Fertilizer Industry
- Polymer Industries
- Systems
- Products
- Life At Rajdeep
- Contact Us
Air Slide
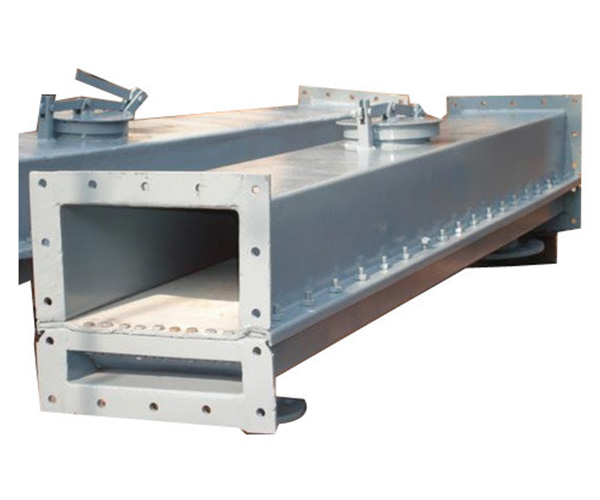
Air Slide
RAJDEEP’s AIR SLIDE will quickly and efficiently convey all materials such as cement, and fly ash. The simple air pressure and gravity combined allow powdered materials to flow like a fluid.
AIR SLIDE are extremely cost-effective and require very little maintenance The Air slide consists of a rectangular chamber separated by an absorbent cloth. The chamber is inclined at a very slight angle (as low as 1.5). Pressured air is injected into the lower chamber which then permeates through the media and “fluidizes” the product. The product then behaves like a fluid and “flows” down the length of the chamber.
UNDERSTANDING HOW AIR SLIDE CONVEYOR SYSTEMS WORK:
Understanding the functionality of air slide conveyor systems is crucial when dealing with the transfer of bulk powder and grains, as they often present the optimal solution for various industrial scenarios.
Airslide systems are among the most efficient and practical options for transporting bulk powder materials. These systems can move hundreds of tons of product across considerable distances by utilizing just a bit of low-pressure air, an aeration bed, and a slight incline (thanks to gravity).
Widely adopted across numerous sectors, including the mining industry, air slides are perfect for conveying uniform dry powder substances such as minerals used in cement, lime, and fly ash production. In the food sector, air slides are instrumental in handling flour, while the chemical industry benefits from their efficiency in moving many types of powders.
One of the significant advantages of air slides is their lack of moving parts, making them a preferable choice over alternatives like screw conveyors, drag chains, and belt conveyors for many applications.
KNOWING THE BASIC AIR SLIDE CONVEYOR SYSTEM FEATURES:
Key structural components of an air slide conveyor system encompass:
– The dimensions of the aeration bed, specifically its width and height, determine the system’s capacity to convey materials.
– Turning boxes (also known as pots) facilitate the redirection of material flow from one direction to another.
– The aeration cloth, typically made from woven permeable polyester, plays a crucial role in the system’s functionality.
– Inspection ports are integrated to allow for visual checks inside the air slide section.
Regarding the operational dynamics of how air assists in the conveying process within an air slide system:
– A fan or blower introduces aeration air through the aeration cloth, creating a fluid-like state for the material.
– Weir plates are employed to modify the depth of the aeration bed, impacting the flow and efficiency of the conveying process.
– Air control valves are instrumental in regulating the volume of aeration air utilized, optimizing performance and energy consumption.
– Dust collection vents are crucial for extracting spent air released from the product during the conveying process, ensuring a clean operation.
HOW DOES AN AIRSLIDE SYSTEM WORK?
In a state of permanent equilibrium, the angle of repose for bulk materials settles into a steady incline relative to the horizontal plane, as illustrated in the diagram below. To facilitate the smooth movement of these materials, conveyor systems had to be designed with an incline that exceeds the material’s angle of repose. Yet, this solution introduced further complexities, leading to the development of fluidized conveying systems, also recognized as air slide conveyor systems or air gravity conveyors.
Salient Features:
- Integrated Design with Bag filter & Air Blower or High-pressure Centrifugal Fan.
- Avoid Dust Generation.
- High-Efficiency System.
- Fluidization cloth to suit the particular application.
- Extremely quiet operation
- No maintenance, no moving parts
- Minimal wear from abrasion
- Special Design to serve the application.
- The system can be integrated with a common control panel.
- MOC: MS / SS304 / SS316
- Size: Up To 500 TPH.
- Length is not a constraint.
- MOC: MS / SS 304 / SS 316
Applications:
- Cement
- Steel
- Non-ferrous
- Powder Chemicals Handling.