- Home
- Company
- Industries
- Pharmaceutical Industries
- Food and Chemical Industries
- Agro industry
- Cement Industries
- Foundry Industry
- Petrochemical Industry
- Detergent Industry Insights: Sparking Innovation
- Steel & Non-Ferrous Industries
- Distillary & Brewery Industries
- Biscuit and Confectionary
- Fertilizer Industry
- Polymer Industries
- Systems
- Products
- Life At Rajdeep
- Contact Us
Bulker Unloading System
Bulker Unloading System
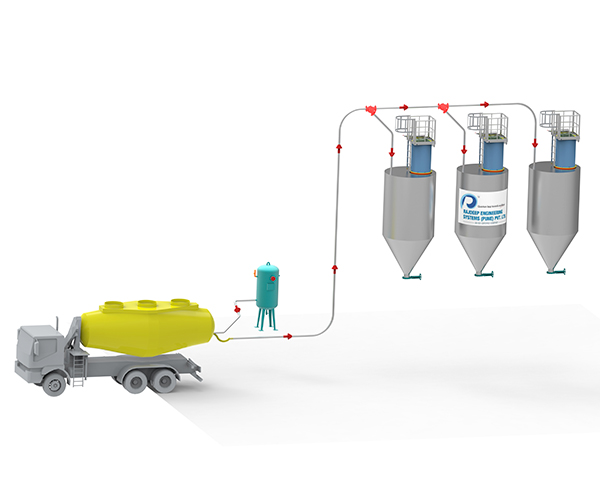
RAJDEEP supplies Bulker unloading System. This system enables to convey of material from Bulker to Storage Silo.
Modern-day recycling and hazardous waste management rely heavily on the storage of large amounts of powders, and the trend in the industry has been stimulated by the need to move production to uninterrupted regimes, minimize manual work with bags, and decrease emissions involved in the work. As a result of this, the powder tankers and bulkers should unload the bulk materials in a safe and fast way.
The air-based tanker/bulker ship unloading solution provided by Rajdeep facilitates the safe and immediate transfer of bulk materials into your plant such as a silo or hopper. A main engine drives a high-pressure prime mover. It thus allows bulkers to be emptied in less than an hour, thus decreasing the need for wharfside power consumption. Designed to fit the demands, our systems have the ability to be customized and produced in various sizes in order to ensure material compatibility. Each gear goes through stringent quality checks before assembly to guarantee its proper and smooth functioning.
Meant to be used from tankers/bulkers to storage silos, we have the pneumatic conveying systems with a capacity ranging from 10 to 25 tonnes per hour where we have the unloading process that is tailored for specific materials.
The material transfer is done in such a way as to be clean and dust-free, and also to minimize dust, and is handled in a considerable quantity of bulk materials.Â
The utilization of bulkers for powder handling has experienced a notable increase as the demand for bulk storage of powdered materials grows, ensuring continuous production and reducing manual handling of small and large bags, consequently minimizing emissions in the work environment.
Rajdeep’s pneumatic tanker/bulker unloading system facilitates the transfer of bulk material from a bulker to vertical storage units, known as silos, within your plant. Powered by a high-pressure prime mover, it efficiently unloads the bulker in approximately an hour, reducing reliance on compressor-mounted bulkers’ availability.
These systems can be tailored to suit your specific requirements and are offered in various sizes based on material properties, with a thorough examination to ensure a robust design. Material transfer occurs effortlessly and without dust emissions, contributing to plant cleanliness during large-scale bulk material transfers.
Connections from the silo line to the bulker line are swift and seamless, accompanied by necessary safety measures to prevent operator errors during system operation.
Salient Features of RAJDEEP'S Bulker Unloading System:
- Conveying Capacity up to 60 TPH.
- Conveyed different materials like lime, Soda ash, cement, Flour, and PTA powder.
- The Bag Dump Station can be put together with the Bulker Unloading System as shown below the scheme.
- The same system can be suitable for unloading material from bags, and jumbo bags.
- Avoid Dust Generation
- High Efficient Filtration System.
- Conveying through Blower as well as Compressor.
- MOC: MS / SS 304 / SS 316 with Industrial or Sanitary Finish
- Simple mechanical hook-ups for air and product conduits to the bulk carrier must be established prior to system activation.
- The design prevents any bulk material from flowing back from the silo/hopper.
- The precisely engineered bulker unloading and storage system guarantees the full emptying of bulk materials from the carrier.
- Thanks to Rajdeep’s advanced dust filtration technology installed on the silos, comprehensive dust management is achieved.
Applications:
- Petrochemicals – PTA Powder unloading.
- Steel and non Ferrous – Lime unloading
- Cement – Cement / lime unloading.
- Distillery / Brewery – Unloading of Grains
- Chemical – Lime / Soda ash / Gypsum unloading
- Food Industry – Flour Unloading.
Benefits:
- Decreased costs for labor, packaging, and shipping
- Reduced reliance on unskilled labor for bag handling within the facility
- Enhanced use of space through compact material storage
- Improved efficiency and speed in bulk material offloading
- Minimized dust creation, promoting cleanliness and hygiene in the facility
- Lowered bulk material loss, with powder transport via tanker, showing a 0.5% loss rate compared to 2.5~5% with bagged transport