In the geography of material handling Lean Phase Conveying emerges as a crucial player, offering streamlined and effective results for the transfer of bulk accoutrements . In this innovative system, air is employed to propel accoutrements through channels, setting it piecemeal from other conveying ways. In this disquisition, we claw into the complications of low- pressure conveying, unraveling its principles, operations, and benefits.
Low- pressure conveying, frequently appertained to as dilute phase conveying, is a system of material transfer that involves the suspense of patches in a sluice of air, creating a admixture that flows through a channel. Unlike thick phase conveying, where accoutrements move in a concentrated, slower manner, dilute inflow conveying relies on advanced air rapidity to keep patches suspended. This fashion optimizes effectiveness in the transport of bulk accoutrements by maintaining a lower material- to- air rate.
One of the crucial benefits of spare inflow conveying is its capability to handle a wide range of accoutrements , from fine maquillages to grainy solids. This versatility makes it suitable for a variety of diligence, including food processing, medicinals, chemicals, and plastics. Whether transporting flour in a bakery or pharmaceutical constituents in a medicine manufacturing installation, lean phase conveying provides a dependable and effective result for moving accoutrements from one point to another.
Another advantage of dilute inflow conveying is its gentle running of accoutrements . The low- pressure air sluice gently suspends patches in the channel, minimizing the threat of damage or declination. This is particularly important for fragile or delicate accoutrements that bear careful running to maintain their integrity. By icing that accoutrements reach their destination complete, dilute phase conveying helps manufacturers maintain product quality and reduce waste. likewise, dilute inflow conveying offers inflexibility in system design and layout.
Unlike thick phase conveying, which generally requires larger channels and more important air compressors, lean phase conveying systems can be configured to fit into tight spaces and accommodate a variety of product layouts. This inflexibility allows manufacturers to optimize their material handling processes and acclimatize to changing product requirements without major structure changes.
In addition to its specialized advantages, dilute phase conveying contributes to spare manufacturing principles by reducing waste and perfecting effectiveness. By minimizing material loss, spillage, and dust emigrations, dilute inflow conveying helps manufacturers conserve coffers and reduce functional costs. also, its nonstop, robotic operation streamlines material running processes, freeing up labor coffers for further value- added tasks.
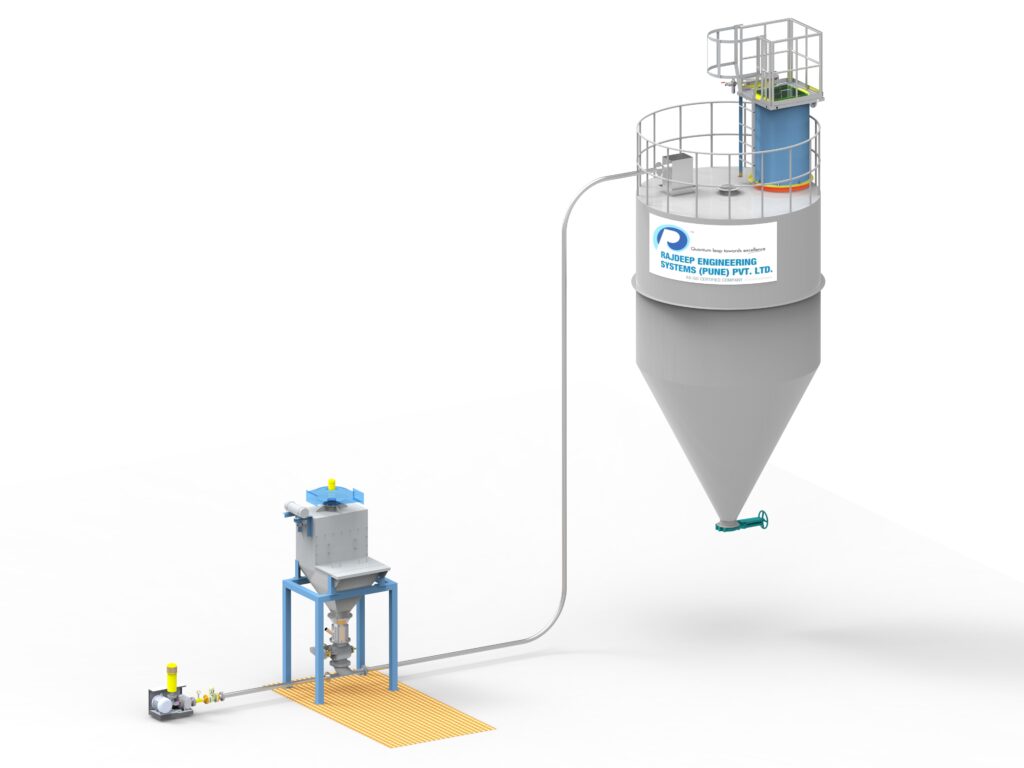
Principles of Lean Phase Conveying:
Air Velocity: Lean Phase Conveying relies on high air rapidity to keep patches suspended. The speed of the air sluice is precisely controlled for optimal material inflow.
Low Pressure Unlike dilute phase conveying, which utilizes advanced pressures, dilute phase conveying operates at lower pressure situations. This results in a lower thick material- air admixture, allowing for briskly material transfer.
Material-to-Air Ratio: The key lies in maintaining a delicate balance between material volume and air volume. This ensures effective conveying without causing material buildup or channel blockages.
Continuous Material Flow: Lean Phase Conveying promotes a steady and invariant transfer of bulk substances through the channel.
Particle Suspension: The air sluice suspends patches, precluding settling and easing the vehicle of colorful flyspeck sizes and shapes.
Applications of Lean Phase Conveying:
Food and Beverage Processing: Gentle running of constituents similar as flour, sugar, and spices.
Plastics Manufacturing: Effective transfer of plastic bullets and maquillages.
Chemical Processing: Precise running of chemical maquillages.
Pharmaceutical Production
Continuous  Operation: Ensures continued product.
Reduced Wear and Tear: lower outfit wear and tear.
Material Transfer Points: preface or junking points of material.
Challenges and Solutions in Lean Phase Conveying:
Material Degradation: Results involve careful selection of conveying parameters and outfit.
System Blockages: Inspection, drawing mechanisms, and system design.
Advancements in dilute inflow conveying Technology
Smart Control Systems Real- time adaptations for effectiveness.
Remote Monitoring: IoT technology for visionary conservation.
Lean Phase Conveying offers a protean and effective result for material transfer in colorful diligence. With advancements in technology, Adulterate phase conveying systems are getting integral in meeting assiduity demands!
Pingback: Auto Weighing and Batching: Precision Engineered Efficiency