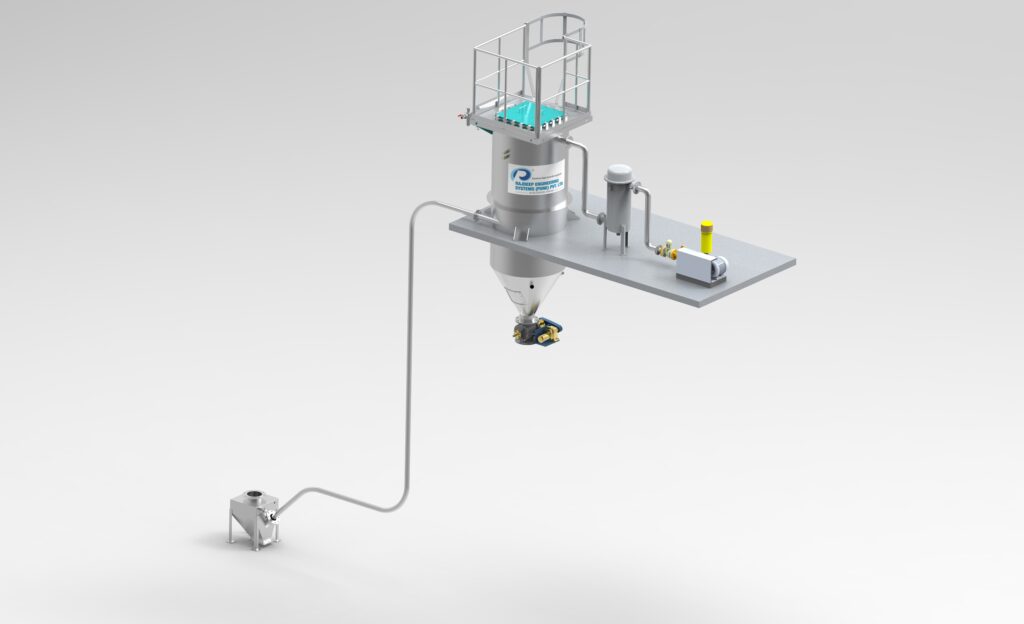
Vacuum Conveying System
A compact and cost-effective solution
Rajdeep’s range of pre-engineered packaged vacuum conveying systems has been meticulously designed to streamline unloading and refilling processes, powered by a venturi ejector or an electric vacuum pump. Additionally, high-performance vacuum conveying systems can achieve dense phase conveying over short distances.
Adaptable design
The modular design offers flexibility, allowing for the adaptation of the suction device to various handling or process equipment, such as sack tipping, drum unloading, BBU Big Bag Unloading, feeder refilling, and reactor loading, among others. Rajdeep’s pre-engineered vacuum conveyors are compact, lightweight, and suitable for both manual and automated operation.
How It Works:
Vacuum Conveying revolutionizes bulk dry material transportation in factories using suction. Through a network of tubing, materials like powders seamlessly move from pickup to process. Systems operate on timed intervals, where the discharge valve releases materials into the process upon sequence completion. Vacuum Conveying encompasses two methods: Dilute phase and Dense phase conveying.
Powder Transfer Systems (PTS) streamline operations by automating material loading and eliminating manual handling of drums and bags. By utilizing pneumatic conveying with vacuum and pressure, PTS simulates liquid-like powder movement, eradicating the need for multi-floor processes. This system is especially suitable for transferring highly explosive or toxic materials, creating a safe environment by removing oxygen from the powder, and incorporating physical barriers to prevent fires and explosions. Installed directly onto the receiving vessel, PTS isolates the vessel during loading, allowing for inert conditions. This technology’s key advantage lies in its ability to separate air from powder, ensuring safe and efficient powder transfer.
Vacuum Conveying System Benefits
Dust-free conveying, with potential leaks contained within the system.
Operation with a vacuum ejector, simply connect to the existing compressed air supply and run the system.
Suitable for use in explosive atmospheres.
Hygienic construction is available.
Compact and lightweight receiving vessels.
Batch or continuous transfer modes.
Additionally, Rajdeep can design and engineer dedicated vacuum transfer solutions.
Applications
Suitable for handling fine and coarse powders, granules, bulky materials, small parts, tablets, compacted particles, and more. Capable of conveying at rates ranging from 0.1 to 8 m3/h over distances up to 40 m. Additional equipment such as inline sifters, magnet separators, and nibblers can be directly positioned in the conveying line.
Specifications
Available in type 304 and 316 stainless steel, with special finishes for the food and pharmaceutical industries. Special designs can handle products with “difficult” flow properties and abrasive characteristics. ATEX execution is available. Automatic filter cleaning during the discharge cycle.
Principle of Operation
Rajdeep’s pre-engineered vacuum conveying systems typically operate on a cyclic basis, conveying for a set time or to a level, pausing while the discharge valve opens and the filters are cleaned. This sequence is repeated as needed. Continuous transfer can be achieved using a rotary valve at the outlet of the receiver.
A certain product is introduced into the line at the beginning of it by various means (suction lances, feeding hoppers, feed screws, rotary valves, and extruders).
The necessary gas flow is generated by the vacuum conveyor located at the far end of the line, sucking the material through the pipeline and into the vacuum receiver. In the vacuum receiver, the gas is separated from the product by flowing through a filter, which rejects the solids. At each drilling cycle, the filter is cleaned intrinsically by an air blast generated via compressed air.
Advantages
- Compact and space-saving
- User-friendly and easy to operate
- Absence of dust dispersal in the environment
- Low maintenance costs
- Suitable for hazardous areas
- Geometric flexibility of the conveyor system
- Empties or fills all process equipment including reactors, dryers, and centrifuges
- Transfers all powders (sticky, fine, non-free flowing, hygroscopic, humid, etc.)
- Safely transports toxic < 1µg/m3 or dust explosive powders < 1mJ
- Charges directly into closed vessels under vacuum or pressure
- Prevention of dust creation
Technical Features To Showcase
- Pressure blowers & Vacuum pumps
- PTS and suction lance fixed on a trolley
- Rotary Airlock Valves
- Transfer Line including Piping, Elbows: Divert Valves
- Filter Receivers
- Dust Collectors
- Control & Electrical Equipment
- Silos & Other Storage Vessels